Welding is a complex craft that requires patience, an eye for detail and creativity. In order to do their job successfully, welders must have an in-depth understanding of the various techniques and practices used in the industry, which includes welding joint types.
According to the American Welding Society (AWS), a joint can be defined as, “The manner in which materials fit together.” The applications of welding are endless, and different jobs require different types of welds and joints.
The term “weld joint design” refers to the way pieces of metal are put together or aligned with each other. Each joint’s design affects the quality and cost of the completed weld. Selecting the most appropriate joint design for a welding job requires special attention and skill.
While there are key differences between SMAW, GMAW and TIG, each of these types of welding uses five common joints to fuse metals.
• Butt joint: Two metals are joined at the edges on the same plane to create a flush surface.
• Corner joint: Two metals are fused to create a right angle, or a corner.
• Lap joint: One metal overlaps the other, creating a lap joint.
• Tee-joint: Two metals are fused at approximate right angles to each other to form the letter T.
• Edge joint: An edge joint is formed when two metals are fused at the edges to join two parallel or nearly parallel metals.
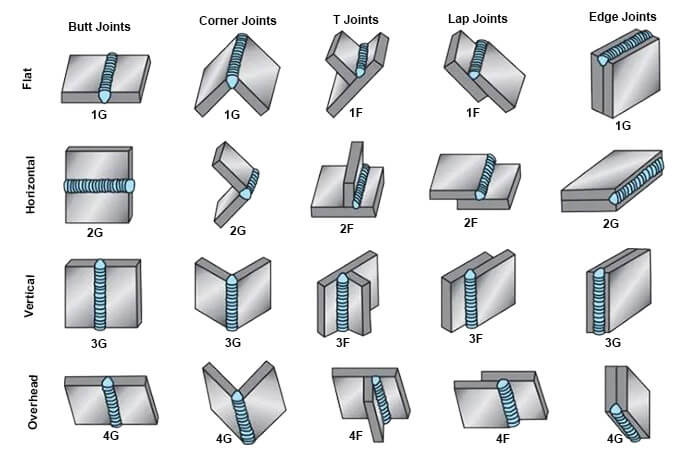
Butt Joint Welding
A butt joint, or butt weld, is a joint where two pieces of metal are placed together in the same plane, and the side of each metal is joined by welding. A butt weld is the most common type of joint that is used in the fabrication of structures and piping systems. It’s fairly simple to prepare, and there are many different variations that can be applied to achieve the desired result.
Butt welds are made in a variety of ways, and each one serves a different purpose. Varying factors include the shape of the groove, layering and width of the gap. Listed below are some typical examples of butt weld joints.
- Square
- Single bevel
- Double bevel
- Single J
- Double J
- Single V
- Double V
- Single U
- Double U grooves
The area of the metal’s surface that is melted during the welding process is called the faying surface. The faying surface can be shaped before welding to increase the weld’s strength, which is called edge preparation. The edge preparation may be the same on both members of the butt joint, or each side can be shaped differently.
Reasons for preparing the faying surfaces for welding include the following:
- Codes and standards
- Metals
- Deeper weld penetration
- Smooth appearance
- Increased strength
In some cases, the exact size, shape and angle can be specified for a groove. If exact dimensions are not given, the groove can be made to the necessary size. However, it’s important to remember that the wider the groove, the more welding it will require to complete.
As the metal becomes thicker, you must change the joint design to ensure a sound weld. On thin sections, it is often possible to make full penetration welds using a square butt joint. When welding on a thick plate or pipe, it is often impossible for the welder to get 100% penetration without some type of groove being used.
When it comes to butt joints, commonly occurring defects may include burnthrough, porosity, cracking or incomplete penetration. However, these can be avoided by modifying the welding variables.
Tee Joint Welding
Tee welding joints are formed when two pieces intersect at a 90° angle. This results in the edges coming together in the center of a plate or component in a ‘T’ shape. Tee joints are considered to be a type of fillet weld, and they can also be formed when a tube or pipe is welded onto a base plate.

Image Credit: Maine Welding Company
With this type of weld, it’s important to always ensure there is effective penetration into the roof of the weld. There are a handful of welding styles that can be used to create a tee joint:
- Plug weld
- Slot weld
- Bevel-groove weld
- Fillet weld
- J-groove weld
- Melt-through weld
- Flare-bevel-groove weld
Tee joints are not usually prepared with groove, unless the base metal is thick and welding on both sides cannot withstand the load the joint must support. A common defect that occurs with tee joints is lamellar tearing—which happens due to restriction experienced by the joint. To prevent this, welders will often place a stopper to prevent joint deformities.
Corner Joint Welding
Corner joints have similarities to tee welding joints. However, the difference is the location of where the metal is positioned. In the tee joint, it’s placed in the middle, whereas corner joints meet in the ‘corner’ in either an open or closed manner—forming an ‘L’ shape.
These types of joints are among some of the most common in the sheet metal industry, such as in the construction of frames, boxes and other applications. There are two ways of fitting up an outside corner joint—either it forms a V-groove (A) or forms a square butt joint (B), as seen in the diagram below.

The styles used for creating corner joints include V-groove, J-groove, U-groove, spot, edge, fillet, corner-flange, bevel-groove, flare-V-groove and square-groove or butt.
Lap Joint Welding
Lap welding joints are essentially a modified version of the butt joint. They are formed when two pieces of metal are placed in an overlapping pattern on top of each other. They are most commonly used to joint two pieces with differing thicknesses together. Welds can be made on one or both sides.

Image credit Science Direct
Lap joints are rarely used on thicker materials, and are commonly used for sheet metal. Potential drawbacks to this type of welding joint include lamellar tearing or corrosion due to overlapping materials. However, as with anything, this can be prevented by using correct technique and modifying variables as necessary.
Edge Joint Welding
In an edge joint, the metal surfaces are placed together so that the edges are even. One or both plates may be formed by bending them at an angle.

The purpose of a weld joint is to join parts together so that the stresses are distributed. The forces causing stresses in welded joints are tensile, compression, bending, torsion and shear, as seen in the image below.

The ability of a welded joint to withstand these forces depends upon both the joint design and the weld integrity. Some joints can withstand certain types of forces better than others.
The welding process to be used has a major effect on the selection of the joint design. Each welding process has characteristics that affect its performance. The rate of travel, penetration, deposition rate and heat input also affect the welds used on some joint designs. The following styles are applicable for edge joints:
- U-groove
- V-groove
- J-groove
- Corner-flange
- Bevel-groove
- Square-groove
- Edge-flange
Due to overlapping parts, this type of joint is more prone to corrosion. Welders must keep in mind other defects like slag inclusion, lack of fusion and porosity, which can also occur.
How This Applies to a Career in Welding
Understanding the physics of joint design is essential for welders, as this allows them to recognize and anticipate the various forces that will be applied to a weldment in the field. Engineers use static and dynamic loading computer programs to anticipate the weldment’s strength requirements.
Today’s welders are expected to understand the types of forces being applied to the weldment and to determine the best joint design to prevent these forces from causing a structural failure. An improper configuration of a weld joint can cause weld and material defects, such as cracking or lamination—and skilled welders must know how to adjust variables to avoid these defects.
Learning to work with different welding joints and weld types takes practice and in some cases, requires the completion of a formal training program, such as the ISO 9606 Coded Welder Certificate offered at EA Institute of Welding. If becoming a welder sounds like the right career for you, this program can provide you with the training you need to get there in just 3 months.
From safe welding practices to principles of welding to complex welding applications, your courses will walk you through key concepts you’ll need to know as a welder—including welding joints. As a graduate, you’ll be prepared to test for welding certifications from organizations such as the industry standard American Welding Society.
No responses yet